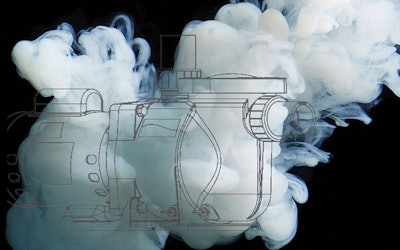
This is the second part of a two-part series on pool pumps. To read the first entry, click here.
As we discussed last time, heat is the main reason pool pumps will fail. To understand why, you first need to understand how an electric motor works along with some basic electrical theory. First, a pool pump motor is made up of copper windings. Copper windings are just small copper wires wrapped in a coil to create a magnetic field when current is sent through the windings. This magnetic field is what causes the motor to spin.
The windings are also where most pool pumps fail.
The windings are insulated with grease that allows current to flow only along the length of the wire. When a pool pump gets too hot (or too old), the grease insulation fails and the current begins to find new, shorter pathways to travel through the windings. Instead of flowing down the length of the wires in the windings, the current begins to short circuit. This will change the amount of current traveling through the motor, and thus, its power.
Voltage, current and resistance are mathematically related. As Ohm's law states, for a constant voltage, current will increase as resistance decreases. This inversely proportional relationship between current and resistance has everything to do with motor failure. As the windings begin to short circuit, bypassing much of the length of wire the current was supposed to pass through, it also has effectively reduced the resistance of the windings. Since current and resistance are inversely proportional, that means the motor will draw more current.
Power in an electrical system is equal to the squared current multiplied by the resistance. This means as the current increases, so does the amount of power (heat) generated within the system. If a motor begins to short circuit in the windings, you'll see:
- A decrease in resistance in the windings
- An increase in current being drawn by the motor
- And ultimately, even more heat generated as a result of the power equation.
This is the beginning of a downward spiral cycle that will eventually result in pump failure.
The extra heat now being generated in the motor will result in even further deterioration of the windings (specifically, the grease that is supposed to electrically isolate the windings from one another), which will result in an even larger short circuit and even lower resistance in the motor windings. This process will continue until one day the pump windings have shorted so much that their resistance is effectively equal to zero. At this point, the current in the motor will attempt to climb to infinity. This is known as a dead short, and it will cause your pool pump to trip out the electrical breaker.
A tripped breaker for a pool pump is never a good thing but there may be multiple reasons why this has happened.
But first, a note: It's possible the tripped breaker could have resulted from a random power surge, or possibly from a water-related ground fault (assuming you have your pump on a GFCI protected circuit, which you should), but these causes are less common.
Why Is My Pool Pump Tripping The Breaker?
If the windings inside the motor are shorting together due to heat or age, and your pump is drawing more current and heating up, you will likely notice it when you discover the pump has turned itself off. This can be from a result of the internal thermal disconnect inside the pump, but more commonly, it will be the main electrical breaker for the pump circuit that you find has tripped out.
By the time your electrical breaker is tripping, your pump is drawing much more current than it was designed to pull. In most cases, once the breaker has cooled down, you will be able to reset and restart the pump. It may run for a long period of time if this is the first instance of it happening, so don't advise your customer to buy a new pump just yet.
Once you discover the pump breaker turned off a second time, you can be reasonably sure you have a deteriorating condition with the pump that needs attention. There still exists the possibility that the electrical breaker is faulty, or that there is a deficiency within the wiring to the pump, causing the tripped circuit breaker.
This is especially true if you use an electrical breaker as switch to turn the pump on and off — while it is very convenient in some cases to do this, it is not a good idea. A circuit breaker is not a switch and using one as such will most likely cause an early failure of the breaker at some point.
Since pool motors draw a lot of current, you cannot just use a regular home light switch to control them. A motor controller switch is a fairly expensive piece of electrical hardware and so some people try to cut this corner by using the breaker itself as the on and off switch. If you do this, and your pump is now tripping the breaker, it is possible that the breaker itself has failed. You would need to test this by replacing the breaker or by using an ammeter to measure the amount of current that your pump is drawing. Compare this value to the manufacturer specification for current draw to see if the pump is now operating out of spec.
How To Stop A Pool Pump From Overheating
Once your pool pump has started to overheat, draw too much current or trip the electrical breaker, there is nothing you can do to stop it from overheating again. If you have had a pool pump failure and you want to prevent this from happening again with a new pump, there are a number of factors you can look at.
Improve Flow Dynamics
One of the biggest problems in the swimming pool industry is pumps that are installed with poor flow dynamics. This has been the bane of pumps and efficiency for decades. Most pumps installed with poor flow dynamics will fail early, but usually past the point where early failure can be specifically attributed to installation error. This makes for a bad situation for the pool owner, and many service technicians will go their entire career never understanding how much plumbing choices affect pump service life.
In a pool plumbing system, the pipe should be as large as reasonably possible with 2 inches being the minimum size for new pools. 1.5-inch plumbing is a fairly serious flow restriction, which allows for less flow than the typical pool pump can generate these days. Hard 90-degree fittings such as street elbows are a major flow restriction — but somehow, they're also extremely common. Choosing the correct size of pump for your application is also very important. Avoid back-to-back fittings within the system whenever possible, as this compounds the turbulence and increases friction losses.
Fix All Leaks
Another big killer for pool pumps: the presence of leaks in the system. This includes leaks in the suction lines of the pool as well as leaks in the equipment directly. Leaks are most common on the equipment pad where most of your day-to-day interaction with the system takes place.
Accidentally moving a threaded connection can cause a small leak to develop, as can improper maintenance or application of gaskets and O-rings. If a leak is very small, many pool owners think repair isn't a priority. What they don't realize is that small leaks on the equipment pad are a surefire way to end up with equipment failing early.
The pump is the most likely cause for concern as there are multiple potential leak points all vulnerable to chlorinated water. In addition to pressure-side leaks that come out of the top of the pump, check for leaks at the main seal. Leaks in these specific locations allow chlorinated water to be drawn into the motor.
The motor draws air from around the middle of the pump (where it connects to the wet-end housing) and any chlorinated water in this area will cause a problem, likely rust in the bearings inside the motor, which results in friction and heat buildup. This heat from friction, combined with the heat is generated by the motor under normal operating conditions, are too much for the motor to dissipate. Eventually, the grease between the windings of the motor start to melt away.
This is the specific cause for most overheating in pool pumps. It is not always obvious that the pump is or has been leaking, but white staining is a telltale sign that chlorinated water has been evaporating on a surface.
You should closely inspect your equipment for leaks on a regular basis. Failure to notice a leak will eventually result in the friction and heat generation described above, as well as noise from the rusted bearings making contact with dry steel.
Eventually, the bearings will seize completely and the motor will no longer be able to spin. Or the motor will short together so much that the current causes the breaker to trip. In either case, by the time the pump makes that awful rusted-bearing sound, you will need to service or replace it.
Rewind The Motor
It used to be that a pool pump tripping the breaker meant you brought your pump to a motor repair shop and a skilled motor repair tradesman would manually rewind the copper windings with new (non heat damaged) ones. This would result in the pump drawing less current since the short circuits in the windings would be eliminated.
This would resolve the problem, at least temporarily, depending on what caused the windings to fail in the first place. While this process used to be common within the industry, hardly anyone still does this. Relatively speaking, pool pumps used to be much more expensive than they are now. Combine that with high cost of skilled labor in motor shops and the end result is that rewinding a motor and buying a brand new pool pump are reasonably close in cost.
If you can get a brand new pump for near to the same cost as rewinding the motor, then a new pump is almost certainly a better option. There are many ways a pool pump can get old and fail, and rewinding a motor would still leave you with an older reconditioned pump. In most cases, unless you can rewind a motor yourself, buying a new pump (or at least a new motor end) is a better option.
Upgrade Your Pump
If you're dealing with a traditional single-speed pool pump, you should consider replacing it — not with the same antiquated technology, but with a new variable-speed pump. Instead of only having "off" and "full speed" as your two-speed settings, a variable-speed pump works just like a light dimmer switch and allows you to run the motor at any RPM speed that you choose.
This is a massive advantage when it comes to electrical usage, since pool pumps can alone make up 50 percent of the average home total power use. Variable speed pumps are so much more energy efficient that they will pay for themselves, in full, in electrical savings within one to three years, depending on how much you normally like to run your pump. While the industry has been slow to adopt this new technology, the electrical efficiency is so much greater than traditional pumps that in many areas it is now law that only variable-speed pumps can be installed on new pools.
Comments or thoughts on this article? Please e-mail [email protected].
Steve Goodale is a second-generation swimming pool expert located in Ontario Canada. You can learn more about Steve, as well as swimming pool construction, maintenance and repair from his website: SwimmingPoolSteve.com.