When the latest hot tub comes out, it's easy to focus on the cosmetic details, to admire the skirt and the sparkly new jets. But as your mom always said, it's what's on the inside that counts, and the spa equipment is no exception. AQUA hasn't checked in with the equipment industry for a few years regarding what's going on inside the spa, and so we decided to see what's new with what makes the spa tick, and also what equipment manufacturers are doing to make servicing the spa easier. Turns out, advances in spa pack technology in the last few years have made life easier for service technicians and hot tub manufacturers alike.
What's New
Not surprisingly, some new innovations have come along in the last few years. PDC Spas is using Gecko Alliance's new spa pack, introduced in 2006. "We use all Gecko equipment, and they've introduced a completely revolutionary set of spa equipment," says Tim Martin, vice president of sales and business development for PDC Spas. "Basically what they've done is come up with some extremely reliable, extremely easy-to-service equipment. It's a whole line called their in.xm line — the industry calls it the xm pack."
The pack is different from traditional ones in a few ways, according to Martin. "We went with it full-production at the beginning of 2006, and it has been wonderful for us," he says. "What they've done with the pack itself is basically sealed all the electronics so that it's not required for a service technician to get in there and play around with anything, and they've also coated them with an epoxy resin, so it eliminates vibration and any of the bad things that can happen with electronics when they are just screwed down to a circuit board, for example. So it's a much more reliable pack."
The in.xm not only has all the electronics sealed, but it also has a number of other innovations, according to JeanLuc Trahan, product manager for Gecko Alliance. "We use custom-made plugs and connectors that were specifically designed for the spa industry," he says. "Basically they are waterproof and are fully rated for their voltage and current ratings, and they also have keying plugs — color keys that allow the installer to only connect an accessory at the location it was intended for. For example, pumps can only be connected to the pump locations on the pack — ozonators, lights, other accessories can only be connected to specific locations on the pack, according to the key on the connector. So that increases reliability — people won't be putting the incorrect accessory on the wrong output.
"As far as innovation is concerned, we have what we call the in.access, which limits access to the components inside the pack to what's necessary for a technician to service," adds Trahan. "There's a door that covers the input lugs where the electrician connects the pack to the home wiring, and that door also gives access to the fuses and nothing else, so all the sensitive electronics are protected inside the pack. With traditional packs, you remove a top cover, and you've got access to everything inside, and what happens is that some service techs can inadvertently damage or break something inside."
The in.xm also has a remote heater, unusual for a spa pack. "Traditionally, heaters are integrated into the pack, but in this particular case, the heater is remote, meaning that it can be installed somewhere else, underneath the spa, wherever it's more convenient for the manufacturer to have the heater, which may not be where the pack itself is," says Trahan.
What About Service?
All the new equipment is great for the industry, but how is it for service technicians? And what are other hot tub manufacturers doing to make sure their equipment is easy to take care of?
Self-diagnostic features on some of the new packs can save dealers time and money by reducing service trips, or by making the pack easier to service once a technician arrives. "The in.xm, because it knows what's connected to it, can also detect what's defective," says Sophie Tremblay, Gecko's technical service manager. "The homeowner just has to read the code to the technician. So before going to the jobsite, the technician already knows what he has to do, so the troubleshooting is already done.
"Codes have been available for a long time, but before, the technician would still have to go on site to troubleshoot it because the spa pack could not know if it was defective or if something that was connected to it was defective. It's a troubleshooting module that actually allows the spa pack to read the current. That way it knows if a pump is defective or if the pack is defective — it won't be the same error code, so a technician would know before getting there what job he will have to do. If you go into our older generation of spa packs, then he would have to bring a few parts, troubleshoot it on site and then replace it. Most of the time, people won't have the parts, and they'll have to go back and make a second trip."
Having the heater located remotely from the pack presents another advantage for techs, according to Trahan. "When it comes time to service the pack, if the heater fails for whatever reason, it's much easier to swap out just the heater than the whole pack, where all the connections are."
The heater is also sealed, the same way the pack is, according to Martin, so there's nothing that the technician has to get into and monkey around with. "It has onboard diagnostics so it communicates its status back to the spa pack, and it doesn't rely on external temperature sensors or pressure switches to verify its proper operation," he says. "It can measure water flow and temperature change within the heater itself, such that you don't require pressure switches to make sure you've got good water flow. It can tell that itself, and any technician will tell you that pressure switches are something that very commonly need either adjustment or replacement. So if you eliminate the pressure switch, you immediately eliminate a typical cause of problems."
if a pump begins to fail, of course its electrical consumption changes, and the pack can monitor that and let the technician know that that's the failing component, without the technician having to test every single thing — the pack is always doing that. It's got a status display right on the pack and it also communicates it to the topside control if a pump or valve is failing."
Second To None
Making sure the spa is easy to service is a top priority for most hot tub manufacturers, regardless of what type of equipment resides under the spa skirt. Many systems today have retained memory, according to Sam Collins, senior vice president at Marquis Corp.
"The service technician can go out and tell what's happened along the way," he says. "They can also upload new software via ports or jacks on the circuit board of the systems; they can run some general diagnostics. If they have a Palm Pilot, in some cases, they can actually get a readout wirelessly, in terms of what's going on and what's the failure mode that it's in." That kind of technology has only appeared in the last few years, he adds.
The reliability and robustness of most spa equipment has been improving over the last few years as well, resulting in fewer overall service calls. "To a large degree, these guys aren't having to make as many trips out with something wrong," says Collins. "Most controls that are on that user panel inside the spa will flash a code if there's something wrong with the unit. Any type of failure in the system will flash in the panel, so the consumer can call the dealer and say, 'Hey, CL is flashing in my spa window, what's wrong?' And the dealer can talk them through a series of steps that they can take to either get it back into steady operation or at least get to the point to say, 'OK, something's wrong with your spa, and I'll send a service guy out.'"
Other hot tub manufacturers are using CD-ROM programs to help their techs service equipment, like Hot Spring Spas' DeTECHtive.
"It's an easy program where you can go in and basically pick what brand, model and year you have, and as you go through and click on those, it brings up the information relative to that spa," says Mark Bettner, director of customer service for Hot Spring Spas.
"For example, one of our spa models is a Sovereign, so let's say you have a Sovereign from 1990. You click that information and up pops a picture and the specifications of that spa. You can go into the parts list, where it lists all the parts used in that spa model, or you do troubleshooting and go into some common symptoms like 'no heat,' and from there it will ask you several questions or it will direct you how to troubleshoot."
The program is helpful to dealers and technicians, Bettner says, because it can either make service calls more efficient, or eliminate the need for them all together if the customer can fix the problem himself. If someone calls in with a problem, "a salesperson who may not be that technical may not understand what it could be," he says. "[But with DeTECHtive] he can very easily tell the customer, 'OK, check to make sure your breaker hasn't tripped, check your filters.' That way if it's something simple, they can resolve it over the phone so they don't have to send a technician out. It saves the dealer time and money, and also saves the customer from getting charged for a service call that obviously they really wouldn't need. So it's a win-win for both sides."
Not wasting service technicians' and dealers' time is high on the list of priorities for all manufacturers. Says Bettner, "We make it very easy for them to service the spa, and they know exactly what to expect."
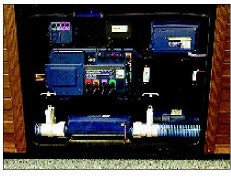