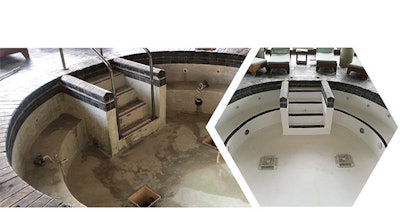
The pool and spa industry desperately needs a new interior-finish alternative, at least according to coatings specialist and inventor Peter Gibson. He passionately believes the inherently corrosive environment of pool and spa water demands an impervious alternative to plaster, exposed aggregates, paint, vinyl and traditional fiberglass coatings.
That's why he has spent years pursuing such an alternative, an effort that led to invention of GlassCoat. Based on technology used by the industrial coatings industry, GlassCoat is a polymeric coating repurposed specifically for the pool and spa industry.
"I've always been focused on finding better ways to solve problems," Gibson says. "Practically everyone in the industry has known about all the various plaster problems for decades, but no one in the pool and spa world knows anything about how it's done in the industrial coatings field."
Gibson, a native of South Africa, started in the coatings industry in 1981 working in his home nation's gold mines, applying various coatings to concrete tanks. "Pools are largely a cement-based industry, but if you look at most other industries, they've been using polymeric materials for decades," he says.
Gibson migrated to the U.S. in 1988 where he continued his work developing and applying a variety of coatings in pools and elsewhere, including spray-on fiberglass surfaces used in a small percentage of pools and spas. Through that experience he came to believe that traditional fiberglass technology was too expensive, too tricky to apply and ultimately unreliable. Despite the many finish products available, the entire industry, he believed, still lacked a suitable coating option.
MOTHER OF INVENTION
He began working on the first versions of the GlassCoat system about 10 years ago, right before the 2008 recession. As was true for many in the industry, the economic downturn stymied his progress, at least for a time. After a few years, as the market improved, Gibson returned to the concept, which he finally introduced two years ago.
"It has been a long, arduous journey, with many iterations to get to this point," he says. "I gained a wealth of knowledge and information along the way. The earlier work I did made the transition from chop fiberglass to GlassCoat much easier. The hiatus of not working with the material somehow made it much easier to conceptualize the process."
RELATED: What's underneath the vinyl in a vinyl-liner pool?
While the GlassCoat material and application process is derived from existing fiberglass coatings, it is different in several ways. Rather than applying the resins and fiber in separate application processes, Gibson developed a formula that includes glass fibers that are mixed with the resin and catalyst and thus sprayed on all at the same time. After surface prep and a primer coat, which uses the same spray system, the mixture is applied using a system designed specifically for the application.
Ultimately, he says, the concept boils down to three major components: the materials, the process and the equipment. "It's a multi-pronged attack to bring it all together," he says. "The glass reinforcement is highly specialized and is added to the resin. Normally the resin is applied separately from the mat or chop fibers. With this system, the whole configuration of glass and resin is sprayed as one homogenous mass."
The materials, he adds, "have been used for steel and concrete protection for a long time. I took the basic concept and redesigned the material and process to suit pool applications."
CONTROLLING COST
While the resulting finish, he says, is far more durable and resistant to fluctuating water chemistry conditions, a significant part of the product's appeal is its competitive cost for both the contractor and pool owner.
"There is a big demand for fiberglass finishes, but the price to pool owners is too high," Gibson says. "The base material cost is higher than plaster to start off with. Also, traditional fiberglass has too many processing steps to bring it into its final finish. This increases labor costs and time spent on a job."
In terms of contractor benefits, Gibson points to a shorter learning curve compared to existing methods of fiberglass application, less labor (three-person crews required for a 4,000 square foot installation), fast application (1,000 square feet in 90 minutes), easy surface prep (typically a light acid wash for existing surfaces) and extremely rapid curing time (pools and spas can be filled less than 24 hours following the application).
"This is a very clean process," he says. "There's no chipping out of old plaster and dust. The only preparation needed is a very coarse acid-etch of the plaster for bond promotion. The rapid cure system also assists in starting the pool up quickly."
As for the pool owner, he says, "The system saves money because it lowers overall operational and maintenance costs. Less pool chemicals are used and the water is easier to balance. They get to enjoy their pools at less cost for longer."
DEVELOPING INTEREST
Using the GlassCoat system does require training and investment in the equipment. As of this writing, four companies are trained to apply the coating.
One of those early adopters is Dave Kubiak, owner of Pool Works, an inground pool builder in De Pere, Wis. Kubiak began using the GlassCoat system at the beginning of 2018 and reports that he's used it on 20 renovation projects, 15 of which were for high-use commercial pools. Learning the process required new skills, he says, but once up to speed, he now sees it as a significant step up from traditional plaster.
"Let's be honest, with plaster it doesn't matter what you add to it or how well you install it, there's always going to be the chance that you're going to be called back because of some problem. There are so many variables that can affect its performance," he explains. "Even though we've only been using this product for a short time, I do firmly believe it's going to hold up much better and will be much easier to maintain."
RELATED: The Fiberglass Revolution
While Kubiak agrees that the installation process is less labor-intensive than plaster or pebble surfaces, it still requires careful attention to some details, such as following application steps to the letter and proper masking of lights and other pool components to protect from overspray.
"It's fairly involved," he says. "Surface prep, for example, is very important, as it is with other types of surfaces. There's a putty mix you can use to fill in voids. The primer is applied with the same machine as the polymer/glass material. It's all very well defined, you just have to have some patience with it at the start."
And, he adds, the aesthetic transformations on some of the projects are eye-opening. "It looks beautiful," he says. "In some cases it's hard to believe it's the same pool when all you've done is replace the surface."