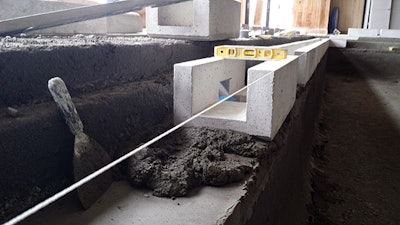
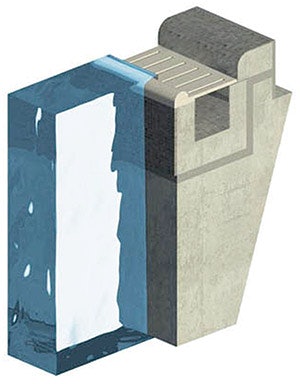
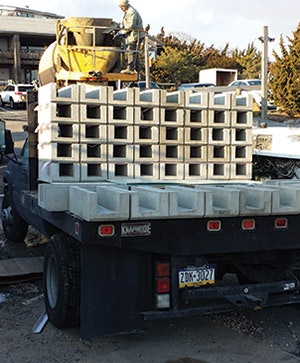
Designer/builder John Talucci, owner of Vision Pools in Downington, Pa., is passionate about marrying old-world craftsmanship with state-of-the-art design and construction. Here he talks about his artisan roots and an innovative twist on gutter systems he hopes will offer builders a previously unavailable option for creating all-tile perimeter overflow details for commercial pools.
I’ve always been proud of my Italian heritage. In many ways, the timeless artisan tradition of Italian masons has been, and remains, the foundation of my work in the pool and spa industry.
Like many in this business, I started young. My dad, Vince Talucci, established Talucci Contracting back in 1980, a grass-roots business that specialized in swimming pool construction. I was 11 when I started at my dad’s side and I’ve been in the business ever since.
My dad initially started out installing vinyl liner pools, which were extremely popular in the Northeast back in those days, but he quickly transitioned to concrete structures due to their infinitely greater longevity and higher degree of technical sophistication. Besides, being Italian, we had concrete in our blood!
From the start, the value system of Old World craftsmanship has influenced everything my dad has done — and I’ve done since. In our case, applying ever-increasing skillsets to creating quality bodies of water proved a formula that both honors our cultural heritage while also setting a fruitful course into the future.
In fact, I think the best way to become innovative and creative is to do so with an unwavering commitment to detail, not all that different from the Roman artisans who discovered concrete more than 2,000 years ago and used it to build some of history’s most enduring and iconic structures.
HARD-FOUGHT, HARD-WON
If all of that sounds “romantic,” (which it is, no question) I’ve always believed that excellence and advancement in most any field must necessarily be steeped in that type of value system. In that sense, my reverence for Italian masonry tradition is one of the most practical items in my tool belt and remains at the heart of our firm’s hard-won reputation.
Let’s face it; constructing concrete vessels that contain water can be brutally hard work. Because it’s so backbreaking, I believe it only makes sense to maximize the positive outcomes by matching the brawn with brains. Yes, we work hard, but to a large extent, to borrow a cliché’, success is just as much based on working smart.
To some, the idea of working smart is perverted into finding ways to cut corners in service of walking away with a few extra bucks at the end of a project. My dad taught me to take the opposite approach. From our earliest days in this business, we actively pursued information that enabled us to generate the highest possible quality. That applied to understanding everything from hydraulics, structural engineering, concrete placement and selection and installation of finish material.
We were so scrupulous, in fact, that for a long time we arguably went to lengths that were probably unnecessary. In in the long run, however, that care of acumen development and application served us well.
In 2004, I struck out on my own and started Vision Pools, wanting to establish my own professional identity and cut my own path. Yet, without the backdrop of the hardscrabble toil of the Italian craftsman, the work we do today would not be possible.
COMMERCIAL EDGES
By the time I lit out on my own, our work had dramatically evolved toward commercial projects. We had always done residential project too, but the percentage of commercial projects has been somewhere between 60 and 90 percent.
The spectrum of projects under the Vision Pool banner has ranged from what some might call “semi-commercial” (meaning condo or apartment pools) and high school and health clubs to high-end community aquatic centers and competition pools on college campuses.
One of the big reasons I’ve always gravitated toward those types of high-use settings is that I believe in the power of water to transform people’s lives, what I call water’s “infinite character.” Naturally, when you create bodies of water in public places, you’re inevitably bringing the vast benefits of water and its widely protean characteristics to large numbers of people.
The notion that I’m using my background, skillsets and artisan passion to deliver aquatic experiences to others is profoundly gratifying. The business success that results — the fact that this work provides a good living for my family and me, and our employees — is a wonderful byproduct.
Yes, commercial projects can be lucrative, but they also come with magnified levels of professional responsibility. (Make no mistake: We apply the same standard of excellence to all residential projects as well.) I believe there is no place for shortcuts in this work. To that point, all of us in the pool construction field owe it to ourselves, and our customers, to ceaselessly pursue perfection. I feel that sense of high purpose with every piece of steel we tie, every piece of coping with set and every piece of tile we lay.
With all that in mind, let’s shift gears into a specific focus on one key facet of commercial pool design and construction, one that has led me to what I believe is a truly nifty innovation.
Gutter Virtues
As I’m sure many people who work in the commercial realm would confirm, the way you treat edges is of supreme importance. It’s on the edge that water circulates from the pool, it’s where bathers enter and exit the water, and the edge treatment to a large extent defines the look and style of the pool.
That’s why building commercial projects among many other things means mastering the art of the gutter.
The primary advantage of the gutter compared to the skimmer is the maximized skimming action. In high-use settings, the amplified overflow effect plays a major role in generating superior water quality. The other big advantage is gutters absorb waves in competition pools, an essential characteristic for so-called “fast pools.”
For those reasons, gutters have naturally become an integral part of commercial design and construction. They are, however, also problematic.
The challenge with gutters starts with the fact there are really only two options: pre-fabricated stainless steel gutters or those formed and poured in place. Granted there are variations within those categories, but in commercial work, you’re going one of those two directions. I’ve done both, almost countless times over the years, and am familiar with the advantages and drawbacks of the two approaches.
Stainless steel gutters have the benefit of being relatively easy to install and are designed for efficient hydraulic operation. The problem with stainless steel gutters, however, is that they corrode over time and will almost inevitably leak. Certainly, maintaining solid water chemistry parameters is helpful as is routine cleaning and inspection. Yet, water being the universal solvent and chlorine the chemical that most readily degrades the material, stainless steel gutters almost without exception will eventually fail at some point, especially at the weld joints, which leads to a range of potential problems.
Another common problem we’ve seen over the years: Stainless steel gutters expand and contract differently than concrete, which will ultimately distress the setting material and eventually result in the gutter dislodging from the bond beam. That differential movement can damage both the gutter and the pool structure, as well invite leaks at the points of separation.
And when exposed to direct sunlight in outdoor pools, stainless steel gutters can become extremely hot and at times even result in burned fingers — a common complaint.
Poured-in-place gutters, meaning those fashioned entirely on site, are by far superior to stainless steel in terms of service life and can be readily finished with tile or other attractive masonry materials. When done correctly, these are, in my view, clearly the gold standard.
The problem: building them is extremely labor intensive and therefore prohibitively expensive in many situations. They also require a level of precision that can be next to impossible for anyone who doesn’t have experience with that type of concrete forming.
Because they’re typically hidden from view, gutter construction is a place where lesser firms will be tempted to cut corners on construction, which can lead to problems such as improper hydraulic function or structural failure. And, as is true with stainless steel gutters, repair or replacement can be extraordinarily expensive.
For years, I found myself thinking we need an alternative that both maximizes the benefits of the two gutter concepts while at the same time eliminating the downsides.
NATURAL FLOW
That’s why it dawned on me: Why not create a pre-cast concrete type of gutter in pieces that you install just like coping? Or put another way, create coping that contains a gutter trough?
The more I thought about it, the more I wondered why such a product doesn’t exist and how beneficial it could be if available. So, we went to work developing the concept.
I liked the idea that with a stainless steel gutter, you simply build a shelf and then simply lay the gutter in place. We wanted to keep that idea, but have the advantages of concrete and tile. The result is a system that produces a concrete gutter, just like a poured-in-place gutter, but using short segments of precast pieces, pred and delivered to the site.
We had already been making precast coping, so we knew that part of the process wouldn’t be a problem. All the while, given my love affair with tile, it was clear that these pieces could easily come pre-tiled, inside and out, and topped with removable tile grates. I was inspired by the idea that we could create something that was easy to install, durable, serviceable and artistically beautiful. That’s all part of why for the finish on the outside and inside of the gutter, we’re using Dal Tile and American Olean, so we have a wide range of tile styles and colors.
The last piece of the puzzle was figuring out how to cap the gutter so that it could be removed for cleaning, a major problem in many poured-in-place systems where the grating is permanently affixed to the gutter. We found a company in Italy that makes a gorgeous porcelain slotted grate tile that would be a perfect fit for our concept. (We also use PVC grating in some situations, which increases the flow into the gutter for high-performance competition pools.)
From there we refined the design, using a 2-inch bullnose on the edge of the gutters to slightly raise the water level about the grates, creating a visually striking deck-level, perimeter overflow, almost vanishing edge, detail. And, it provides a perfect handhold.
We wanted it to be easily installed so we created pieces that are two feet long and weigh only 28 pounds; easily lifted in place. There’s also a 10-pound cap piece that sits on top of the gutter on the deck side, providing an easy interface with the surrounding deck surface.
The system, which we’ve named Natural Flow, is made with Portland cement, mesh reinforced with a small amount of Perlite admixture, which helps keep the weight down. On site, the pieces are simply set in a mortar bed, just like a standard coping. The grout joint between the pieces are filled with an 1/8th inch of Sika 1A sealant, a wonderful product we use creating most of joints for a variety of applications.
Plumbing is similar to a stainless steel pool where you’ll have one or two, or as many as you like, places where the water flows through a 3-inch connection in the bottom of the gutter to a trunk line and then into to a surge tank. It can be configured any you want, but our recommendation calls for two or more drop-out connections on the long side of the pool, every 25 to 30 feet, and one on each end, the idea being to create an even draw on the pool.
DOWN THE LINE
We developed this system for our own use, but have experienced such a positive response that we are now making it available to other builders. We’re still in the early stages, having launched the product line this past fall, but have already had it specified into a number of projects currently under construction or about to start.
The early response we received from designers, project owners and other builders has been truly overwhelming. You never know what will happen when introducing a new idea, but at this point, I’ve become confident we’re really onto something special, some have even called it a potential game changer. We’ll see.
When we started down this path, it wasn’t my intention to necessarily become a product supplier, but at this point, that does appear to be where we’re headed. However widespread Natural Flow becomes, I’m extremely proud of this innovation and hope that it results in more affordable and superior quality installations.
Certainly what we’ve done is nowhere remotely near the kind of innovation seen in ancient Rome when they built the aqueducts and the world’s first paved roads, but I do like to think we’re being inventive in the same tradition of creativity and excellence that is at the heart of the true artisan, past and present.
Comments or thoughts on this article? Please e-mail [email protected].