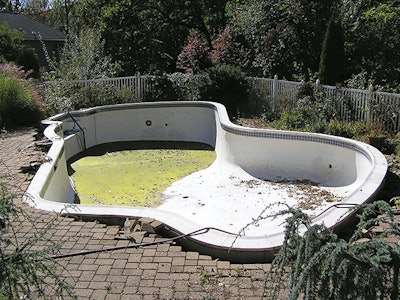
In the spectrum of pool and spa construction failures, pools shells that pop out of the ground can be the most severe, sometimes requiring complete demolition and removal of the damaged vessel. To help builders steer clear of those disastrous situations, as well as more minor damage, AQUA Senior Editor Eric Herman runs through the fundamentals of mitigating the effects of hydrostatic pressure.
External hydrostatic pressure can potentially impact any inground pool and/or spa structure. In fact, the only vessels that are immune to the problem are those resting entirely above grade. Beyond that basic tenet, some in our industry labor under potentially harmful misconceptions.
For example, the perception that the weight of a concrete pool offers a counterbalance and thus a measure of safety is misguided. The notion of a hydrostatic relief valve as a cure-all is also off the mark.
Builders who work in areas with high water tables — meaning those that rise above the lowest point of the pool structure — must contend with the challenge early on in the excavation process, according to geotechnical engineer Neil Anderson, principal and senior engineer at Neil O. Anderson and Associates, A Terracon Company, and a leading authority on the subject of soils and groundwater issues.
"When you dig a pool in an area with a high water table," he says, "you have to lower that water in order for your excavation to be dry so that you can construct the pool. This is true for a fiberglass pool, a vinyl liner pool or a gunite pool; it impacts all types of construction, except aboveground pools."
While the solution to high water tables during construction boils down to common sense, doing so does require effort and expense. "You install well points and run a pump to constantly draw down the water," Anderson says, "or you can do it by way of a sump where you excavate a hole lower than the pool, install a slotted pipe backfilled with gravel and drop a submersible pump in to remove water infiltrating in from the sides — either way you're doing the same thing."
WHAT'S HAPPENING
While a high water table becomes immediately apparent in the initial phases of construction — building a pool in a hole full of water is fundamentally impossible — the way that hydrostatic pressure might impact an existing vessel may very well come as a surprise to many.
Diagrams courtesy of Neil O. Anderson and Associates, A Terracon Company
Anderson explains: "What some people don't realize is that it's not about the volume of water surrounding the pool, instead it's only about the height of the static water level surrounding the pool compared to the water level inside the pool. You can have as little as a 1/8th inch of water around the pool and it will pop so long as the water around the pool is continuing to be fed as the pool shell is lifting. This how rainstorms can 'pop' a drained pool shell."
This all-important inequality between water inside and outside the pool structure is known as "differential head." It can occur when a pool is drained for winterizing, repair or replacement, while at the same time the water outside the pool rises due to a storm, snow melt or even seawater intrusion.
Because concrete pools are far heavier than fiberglass or vinyl pools, the differential head required to cause lifting and damage is somewhat greater, but probably not as much as most people would think. According to Anderson, a fiberglass pool might start to float with just a couple inches of differential head, while a gunite pool will require as little as 18 inches, which is still significantly less than most people realize.
"I have seen numerous concrete pools where the water is down two or three feet over the winter and when a spring rain comes or the snow melts the pool will float or pop," he explains. "You can pop a gunite pool and you can pop a fiberglass pool anytime that head outside the pool rises sufficiently above the water level on the inside, irrespective of water volume."
As for vinyl liner pools, the same basic principles apply, although the resulting damage is different. A vinyl pool in which the water level has been lowered for winterization may see a temporary hydrostatic head condition when water surrounding the pool rises due to a rainstorm or snowmelt.
"When that condition exists," he continues, "water trapped around the pool will infiltrate down through the soil and attempt to come up under the floor as it seeks to equalize pressure. This causes blisters in the liner floor. It's very common because it can happen with only a couple inches of differential head or height between the inside and outside of the pool."
SEEKING RELIEF
Traditionally, pool builders have turned to the ubiquitous hydrostatic relief valve as an inexpensive insurance policy, and as a general statement every pool should have one or more.
"In a concrete pool, you're supposed to have a hole in the bottom of the 'boat' in the form of a hydrostatic relief valve," Anderson explains. "When you have differential head where the water outside the pool is higher than the water inside, the valve theoretically allows the water to flow into the pool as it seeks level."
As basic as that may sound, some builders nevertheless run into trouble when they assume that because they are working in bone-dry ground conditions they don't bother to install one, or they simply forget. Added to that, there are basic errors in construction that further exacerbate the problem. Says Anderson: "What often happens is during construction the builder creates an excavation ramp and then doesn't install a hydrostatic relief valve. During a storm water will gather where the ramp was located and then infiltrate around the pool. The shell will pop even though there's no high water table."
For builders who do religiously install hydrostatic relief valves, Anderson adds there are situations in which they fail to open properly or don't relieve pressure quickly enough. "We've seen pools with hydrostatic relief valves still pop out of the ground," he says. "That can happen because the valve stops working for some reason or the valve doesn't allow water to enter the pool at the same rate as it's flowing into the area around the pool.
"I looked at a pool in Napa, California, where the builder had left two holes in the bottom of the pool, but the pool lifted out of the ground anyway," he recalls. "It was simply that during a rain the water flowed around the pool faster than it was entering the pool through the two holes."
Added to the slow-relief valve issue, there are simply times the valve fails to work at all, leaving even extremely large pools exposed to potential damage. Don Danley of D & L Pools in Hannah City, Ill., has been in business for 45 years and has extensive experience dealing with ground water in the greater Peoria area, where levels can vary significantly from place to place. In almost half a century of pool work, he's seen it all.
Danley recalls one situation in which a simple valve failure resulted in one of the worst scenarios he'd ever encountered, where a large pool came out of the ground with the deck still attached. "They drained the pool, but the hydrostatic relief valve was somehow jammed. When they came back the next morning, the shell was sticking out of the ground at about a 45-degree angle," he recalls. "We were asked, 'How can we put this back in the ground?' I told them they weren't putting it back in the ground but instead tearing it out and putting in a new one."
SITUATIONAL AWARENESS
By contrast, there are some situations where the resulting damage is so subtle pool builders are left completely unaware, even during the construction process.
"I once looked at a pool that had lifted to create a three inch differential between the deep end and the shallow end," Anderson recalls. "It was right next to the San Francisco Bay, so we knew exactly where the water table was; about 15 feet below grade. When they excavated the skimmer, they backfilled with loose soil while the rest of the soil around the pool was clay and didn't allow for any drainage. They gunited the pool and then had a big rainstorm, which filled in the skimmer excavation and then worked its way around the pool."
What happened next left the unsuspecting builder bewildered: "Unbeknownst to the builder it lifted the pool on one end and no one noticed," Anderson explains. "They went ahead and finished the pool, installed all the decks around it but when they filled the pool it was uneven. There was about a two-inch void under the deep end of the pool where it had lifted."
According to both Anderson and Danley, the key to preventing damage is to first be aware of the site conditions and make appropriate provisions. "We built a pool downslope at the end of a cul-de-sac where water from the adjoining properties was running like a river through ground beneath the clients' home," Danley recalls. "Fortunately we knew what we were up against. There, we ran two slotted pipes below the pool to collect the water that was rapidly flowing into the pool area and directed it to a relief point on the back of the property. We never had a problem after that."
Pools such as that one, located at the bottom of a hill where groundwater is conducted downslope through subsurface bedding planes can create serious problems, he adds. "You can always make provisions where you tie several well points together to pump, but sometimes it gets to the point where you wonder how many pumps is this going to take, because the water flowing like a river."
THE DRAIN GAME
As indicated earlier in this story, the drainage system required to alleviate soggy site conditions during excavation will often consist of a layer of gravel with a sump at the lowest point and a submersible pump. Once the pool is completed the pump is removed or simply sacrificed and buried with no further thought given to external ground water. However, if the pool is ever drained for maintenance, or the water level drops during winterization then there is a potential for popping. The best way to prevent this is to install a permanent sump off to the side so that you can see what the external hydrostatic water level is and if necessary you can drop a submersible pump into it to lower the water level before draining the pool.
"The way to avoid liner blisters is to prevent the external water from ever reaching that level where it's higher on the outside of the pool than it is on the inside," Anderson says. "The way you do that is by creating good drainage around the outside of the pool.
"From an engineering standpoint it's a very straightforward calculation," he adds. "We know the rate at which water can flow through gravel and we know how fast water can flow through a given sized hole. In a situation where we're looking at rapidly rising water, we might specify six inches of gravel and three hydrostatic relief valves.
"At a minimum, I would recommend that the gravel beneath a pool extend at least to the sides. That might work for as much as 99 percent of the situations we see. But there are those projects that might be in a flood zone of some kind and when it rains enough without proper drainage, it could still pop the pool. Anytime you start guessing, there's risk. Whenever in doubt about possible effects of external hydrostatic pressure, or other soils related issues, it's always best to bring in an expert."
Staying Put
Any builder in a region with a high water table must consider the effects of hydrostatic pressure on a pool. One fiberglass pool manufacturer has developed a creative system designed to keep pool shells in place even when groundwater is high and the pool is partially or completely drained.
There is no debate; it's a law of physics. All pools are vulnerable to differential head — when the water in the pool is lower than the water creeping up around it (see main story). Which is why one fiberglass pool manufacturer, Thursday Pools of Fortville, Ind., has decided to tackle the issue of hydrostatic pressure head on with a couple of nifty innovations the company believes permanently solves the problem.
A POSITIVE APPROACH Known simply as the Fiberglass Pool Anchoring System, the concept couples a clever relief valve system with actual, physical anchors to hold pool shells in place in the presence of hydrostatic pressure.
Its inventor, company founder and CFO, Bill Khamis, was inspired by an extensive background in home construction and marine fiberglass tooling to develop the anchoring system. "I've been in the fiberglass industry for 30 years and about 20 years ago we also got into building high-end, custom homes," he explains. "Those homes started at $2 million dollars, which among other things meant that most of them included concrete pools. During that time, really within just three to five years, we started seeing issues with concrete pools, including hydrostatic valves leaking. They'd get fouled with sand and you'd have to dive the pool to fix them. Our goal was to develop a solution that ultimately generates better performance and greater confidence on the part of the homeowner."
REPOSITIONING THE VALVE The system Khamis and his company developed includes a patent-pending hydrostatic relief valve known as the Geo-Hydro Valve. "It started when we were installing my own fiberglass pool," Khamis recalls. "When I asked about hydrostatic valves I learned they're not used in fiberglass pools."
The problem, he explains, is two-fold: "One part of it is the difficulty in accessing the valves for maintenance. As we studied hydrostatic relief valves, we learned how easily they could be fouled with sand or fines that enter the pool when ground water pressure is relieved by the valve or by debris that naturally settles at the lowest point in the pool. With valves installed in the main drain sump, you have to dive the pool to clean or replace them. Not only are they difficult to maintain they also happen to be placed in the one spot where they're most likely to encounter problems."
The other challenge, he explains, "is the difficulty installing them because you're trying to do a very critical backfill around the valve, which is next to impossible once you've lowered the shell into place."
The solution Khamis lit upon was elegantly straightforward; simply reposition the valve from the main drain to the sidewall just above the lowest point in the pool. By doing so, he explains, the valve is both easy to install and easy to maintain or replace.
"It takes a single glue joint to install," he says. "And, since the builder is already backfilling the around the sides of the pool, there's no problem with that aspect of the installation."
The assembly also includes a check valve so that if there is a problem with the valve, water will not flow out of the pool.
Khamis is so excited by the valve concept that he sees broader applications in gunite pools as well, especially for those that don't include a main drain. "We don't advocate the use of main drains," he explains. "In our research, we've discovered that a great many engineers and builders see no real need for a suction outlet at the pool's bottom. In our pools the circulation needed for chemical mixing and heat distribution is handled by eyeball and butterfly returns. By placing the valve on the side of the pool at the lowest point, you no longer need to locate it in the main drain sump.
"And that," he adds, "will work for any type of pool construction."
"It's such an obvious concept I've wondered why no one else has tried it," Khamis says. "My guess is that they were probably trying to somehow glue the mesh on to the shell, which probably wouldn't work."
Relying on his experience in fiberglass manufacturing, Khamis sought what he believes is a far more reliable solution. "We worked closely with Owens-Corning, who we've worked with for over 35 years, and Interplastic Resins to solve the problem," he recalls. "We use a special glass fabric material and we developed a special weaver where the fiber is not attached to the wall but instead comes out of the wall as part of the intrinsic fiber structure. These anchors are part of the shell. The material is made of silica, obviously very high end; it's never going to deteriorate in the earth."
The shells are shipped with the fabric anchors rolled up on the sides, which are subsequently extended into the surrounding fill during the backfilling process. Depending on the depth of the vessel, the shells come with one, two or three layers of fabric, which extend 24 inches laterally into the fill.
The company specifies the use of quarter- to half-inch chip rock for the fill. "That way water is easily conducted around the shell," Khamis explains. "That's important because in the case of hydrostatic pressure, you want the water to move quickly toward the hydrostatic relief valve.
"The fabric anchors also provided the added advantage of preventing back fill material from moving toward the bottom of the pool," he adds.
"Because we had to have complete faith in order to provide a warranty, we tried everything we could to get the system to fail" he says. "Without exception it worked perfectly and we are now confident that these pools will not float or pop in the vast majority of conditions."
In addition to providing what the company now believes is a foolproof system, Khamis notes that they are committed to educating dealers how to install it. "For as effective as the system may be," he says, "there's no substitute for a competent builder, which is why we're devoting considerable time and resources to training and dealer support."
Comments or thoughts on this article? Please e-mail [email protected].