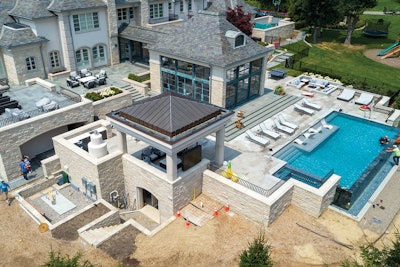
Old money and new money coexist nicely in Detroit's Bloomfield Hills area. Descendants of Motor City's automobile aristocracy share parks, lakes and other neighborhood amenities with A-list celebrities and NHL players. Residences are often commercial in scale, and construction timelines are no exception.
When money is no object, architects and engineers are involved at every level, even for something seemingly simple, like a back patio addition. But a "back patio" addition in Bloomfield Hills is likely to include a heated pool, spa, outdoor kitchen and more. These projects require a special kind of builder — as well as specialized subcontractors.
Center Line Heating and Cooling grew with the city of Detroit. Today, the 25-person firm focuses exclusively on custom homes in the 10,000- to 55,000-square-foot market.
Long-standing relationships with the area's most exclusive builders and subcontractors yield constant demand for intricate, multi-faceted mechanical systems. This work regularly requires Center Line to be adept at all facets of mechanical work, from HVAC to pool heating.
THREE-GENERATIONS OF GROWTH
"My grandfather founded Center Line in 1936," says Jeremy Gillette, owner of the company. "In the '90s, we specialized in hydronics because that's the way the custom home market was moving. We're big enough to handle any home but small enough that I have personal oversight on each project."
Recently, the company purchased a 12,000 square-foot facility. The additional space has allowed Center Line to stock many commonly used products, which is especially convenient for hydronic jobs that often take specialty components.
"We've implemented a new Fishbowl inventory management system, which has had a learning curve, but it's been well worth it," continues Gillette. "We have a barcode system, so everything is scanned in and out. It makes ordering material easier, too."
"Center Line has done business with HS/Buy Van Associates for 25 years or more," says Gillette. "Jarrett Armstrong, vice president of commercial sales, has been a great resource. On the engineering side, we work hand-in-hand with Kaiser Consulting."
A recent Center Line project was a perfect example of how long-developed, collaborative partnerships yield extraordinary results.
Center Line at work on the heating system for the home's 36,000-gallon pool. The system uses Aspen boilers with titanium heat exchangers.
JUST A BACK PATIO
Thomas Seabold & Associates, one of the best-known custom builders in the Detroit area, approached Gillette about an outdoor living addition to a 30-year-old, 25,000-square-foot home in Bloomfield Hills. The design-build project was to include three patio levels, an outdoor kitchen, pool, spa, bathrooms and a solarium. The pool was to be heated and each level of the patio to be snowmelted.
"After the builder had final plans, it was up to me, Armstrong, and Mike Kaiser at Kaiser Consulting to design the hydronic pool heating, snowmelt and radiant systems," says Gillette. "We wanted all heating loads to draw from a central boiler plant."
Armstrong suggested the use of Aspen light commercial firetube boilers, made by U.S. Boiler Company, and assembled the list of needed tekmar components to control the whole system. It was critical that the new system tie in seamlessly with the home's existing home automation system.
PREMIER POOL BUILDERS
The 36,000-gallon saltwater pool, and the spa attached to it, were built by Gillette Brothers Pool & Spa (no relation to Jeremy Gillette).
"The owner had some very specific requests for this sport pool," says Carter Gillette, vice president and part owner of Gillette Brothers.
"It's 39.5-by-20 feet. One side is 3.5 feet deep. In the middle, it's 4.5 feet deep, and on the other side, it's 3 feet, 4.5 inches deep."
Gillette Brothers is a 40-person company focused on high-end work in the Oakland County area. Most of their projects include negative-edge, perimeter overflow pools — though they still build some pool and spa combos.
These two 399 MBH Aspen light commercial boilers handle snowmelt, radiant, pool heat and DHW.
POOL HEATING WITH BOILERS
"I've worked with Carter and Wes Gillette for a long time," says Jeremy Gillette. "They do amazing work, and we're collaborating with them more frequently than we used to because what we do and what they do are increasingly interconnected."
Over the past 20 years or so, heating pools with boilers has been growing in popularity, according to Jeremy Gillette. This is due to new boiler technology and the fact that using boilers has advantages over stand-alone pool heaters, in certain applications. Heating a pool with boilers makes sense when a boiler installation is already planned for the property. By upsizing the boiler(s) to include the pool, gas lines and venting only need to be provided in one location. Space savings and higher efficiency are also advantages.
Considering the large heating load of the pool on this project, a boiler approach made sense. The owners want to maintain 92 degrees Fahrenheit pool water for nine months of the year, without a cover. To deliver so much heat, Center Line installed an 800 MBH Advanced Industrial Components (AIC) titanium shell-and-tube heat exchanger, which transfers thermal energy from the boilers to the pool. One hundred eighty degrees Fahrenheit supply water is pumped from the boiler to the heat exchanger.
"The heat exchanger is custom made, and we selected titanium for its corrosion resistance, which is a big consideration when heating pool water," says Gillette. "The shell-and-tube design of the heat exchanger is easier to service and clean than a plate-and-frame model of the same capacity. Also, because the channels inside a shell-and-tube heat exchanger are larger, it also provides lower pumping resistance than a plate-and-frame model. Once we fired the Aspen boilers and turned on the pool zone for the first time, the body of water went from 65 to 84 degrees Fahrenheit overnight."
The spa is not heated independently of the pool. The installation is a one-system pool-spa. When the owners want to use the spa, valve actuators divert water to and from the heat exchanger to flow through the spa, which heats it significantly beyond pool setpoint temperature.
UNDERGROUND MECHANICALS
Center Line vented the two, 399 MBH Aspen light commercial boilers individually, through the only exposed wall in the mechanical room. Offering up to 96% efficiency and with a combined turndown ratio of 20:1 via the onboard cascading Sage controls, the dual Aspen approach offers outstanding efficiency and flexibility.
"We started installing U.S. Boiler Company products about seven years ago, in large part due to our great relationship with HS/Buy Van," says Gillette. "Jarrett is always quick to help us on hydronic designs and controls. The Aspen is a proven product for us, and Buy Van has parts in stock if something should ever need repair with a fast response time."
To protect the entire hydronic system from freezing, including the pool heat exchanger, radiant loops and snowmelt zones, Center Line installed a 15-gallon Axiom glycol feeder. A 35% Dynalene glycol mixture is used throughout.
MORE ELBOW ROOM
Before this past summer, Center Line Heating and Cooling headquarters had been in the same 4,000-square-foot shop since before World War II. With the purchase of their new shop in April 2023, and the implementation of the Fishbowl inventory system, they're now poised for further growth and faster response times.
"We're now in a commercial complex instead of a neighborhood, which makes deliveries, etc., much more convenient," says Gillette. "Here, we can do a little bit of prefabrication, but most of our projects are so large that components need to be assembled onsite, coordinating with the other trades."
"The new warehouse and inventory system have already proven to be a great advantage," says Gillette. "We're able to stock installation materials and maintain accurate job costing to ensure that we're quoting properly. That's especially important right now, as we're conducting another job almost identical to this one, not to mention 10 other hydronic projects."
This article first appeared in the February 2024 issue of AQUA Magazine — the top resource for retailers, builders and service pros in the pool and spa industry. Subscriptions to the print magazine are free to all industry professionals. Click here to subscribe.