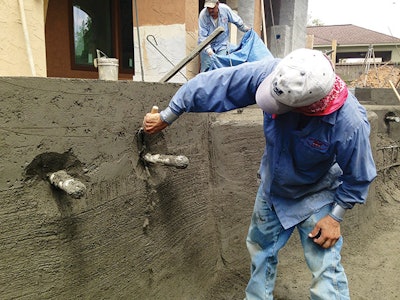
Modern Method Gunite of Houston, Texas, is rare among subcontractors in that the company installs both gunite and surface material. According to Edgar Sanchez, a second-generation company manager, by combining both phases, their crews have learned a number of practical lessons that maximize the efficiency and quality of their work.
Although the swimming pool industry is not widely known for clever innovations, my experience growing up in the industry has taught me over and over again that implementing new ideas can translate into sustained success.
That story begins more than three decades ago when our company, which started in California installing gunite shells throughout the state, moved to Houston in 1981 in search of new opportunities in what seemed to be a relatively untapped market.
My dad, Cesareo Sanchez, was part of the management team for the company that in those days consisted of two crews and 24 employees. Unfortunately, about a year or so after they came to Texas, the local economy crashed and they were left looking for ways to sustain the business. As it turned out, the pressure of sustaining the company in a down market would drive a culture of adaptation that has sustained us ever since.
The first move was to open a division in the more favorable economic landscape of Boston, Mass. Shortly thereafter, my dad and his cohorts developed and patented the first-ever volumetric mixing system also known as “Mobil-Crete,” an auger-driven, two-phase delivery system that enables gunite applicators to pre-load the unit with sand and cement rather than having to stack piles of cement bags and sand and load the mixer by hand.
The system enables gunite firms to mechanically and precisely mix gunite with the same precision found in the shotcrete, or wet-mix process, without the issues that come with cement truck batches when site conditions or weather pre-empt immediate application.
DIVERSIFIED INTEREST
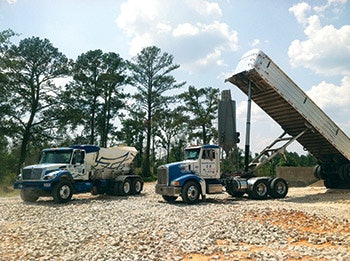
The development of that system was a quantum leap forward that enabled the company to surge forward financially. To this day, we’re very proud of the fact that volumetric mixing technology has become the standard for most of the gunite application industry.
One of the things we did to stay ahead of the curve in those days was to start selling moss rock, flagstone, tile, white cement and all the equipment associated with those products. And we started private labeling trowels and other items for other companies in our market.
The original idea was to start a buying group, but nobody else had the capital to make that work, so we just started buying equipment and materials ourselves and sold it to other firms who were looking to expand and improve their own operations.
Of course, these days you can find all sorts of sellers of stone and concrete materials, but back then the availability of stone material was far more limited. We started working directly with quarries and other suppliers to supply the market with products that weren’t readily available, which neatly dovetailed with the vast creative expansion the pool industry experienced in the ’90s — an expansion that continues to this day.
AGGREGATE OPPORTUNITY
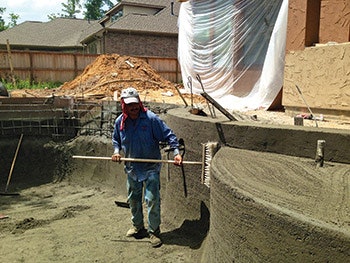
Shortly after I came onboard, we were approached by the folks at Pebble Technology to start working with their products. At first, our idea was to step in as a wholesale distributor, but that’s not what they had in mind. Pebble Tec long had their distribution method in place, which is entirely focused on licensing applicators.
That prospect led us to several rounds of critical analysis of the surface application business. In all his infinite wisdom, my dad charged me with the task of defining all the reasons why we shouldn’t get into surface application. After a period of extensive analysis, the main objection I came up with was that when you look at traditional plaster applications, it’s painfully obvious that if there’s any problem with things like surface cracking, staining or etching, the applicator is the first person held accountable, even though those problems can be attributable to a host of factors that aren’t really the plasterer’s fault. As a business model, surface application looked very problematic.
Although I was skeptical about the overall plastering industry, we also saw that Pebble Tec was in many was a different animal compared to the rest of the surfacing industry. As part of our due diligence, I flew to Phoenix and spent time looking at past projects and saw firsthand what the pebble concept was really all about.
After a considerable amount of research, I changed my mind. The nature of exposed aggregate/pebble surfaces combined with the support that Pebble Tec afforded their licensees painted an entirely different picture of the surface application process. I went back to my dad and suggested this was something we could and should do.
In 2002, we became a licensed Pebble Tec applicator. At that point, as far as we knew, we were the only gunite company working in both the placement of pneumatic concrete and surface applications. (September of this year will mark our 11th anniversary working with Pebble Tec.)
Naturally, once we signed on with Pebble Tec, we had to master the process. Instead of bringing in new people, we charged some of our experienced foremen to take on surface application and started a process of cross training that continues to this day.
NEW SYNERGIES
What no one could’ve possibly predicted was how applying surface materials would show us the synergies possible between installing the gunite substrate and the finish material.
The first thing we learned involved the way we “finished” the gunite surface. Our approach had been to leave a flawless gunite surface so it looked like you could fill it without plaster and have it look perfect. Even though we knew our work would be covered with a finish material, our desire for perfection meant that we wanted the gunite shell to look as pristine as possible with precisely finished contours and smooth surfaces.
We quickly discovered that wasn’t the best approach when it comes to applying surface material. Our gunite shells may have looked perfect, but a smooth finish wasn’t providing the best surface for adhesion of the pebble material.
Seeing the need for maximum contact with the pebble material, we soon learned it was better to go over the gunite with a deep-broom finish that didn’t look as pretty but was far better for the surface applicators. As obvious as that might seem in hindsight, it was something we realized only after we trained crews in both processes.
We also learned the importance of notching around main drains and wall fittings, again something we hadn’t previously considered. We found our surface installation crews had to actually jackhammer out around fittings to accommodate the surface application.
Now, as a result, we leave more space around these fittings, not necessarily wider but deeper spaces where the finish installer can easily pack in more material.
We also found that for all of our effort to shoot perfect gunite shells, when it came to light fixtures, we weren’t properly shooting the space underneath — an easy thing to miss because it’s not so visibly apparent. In practice, it’s a simple matter of the nozzle man bending down and making sure the underside of the fixture is surrounded by solid and reliably placed material.
These are incredibly common mistakes, stuff we saw in our gunite work and the work of others. But because we were living with the consequences of the gunite process, we quickly made changes.
STAYING FRESH
We also realized it made sense to cover the more difficult parts of the structure first, meaning we don’t leave the steps and benches for last. There were times in the past that we did those more challenging parts last and in some cases had no choice but to use rebound because the truck and rig had already left — which was short sighted on our part.
Frankly, it just makes sense to install the more detailed work first, before the heat of the day, which makes a huge difference in morale and the crew’s energy level.
Along the same lines, we also found it makes sense to send a crew ahead of time to “string out” the trickier details rather than setting those dimensions later in the day when it’s hot and everyone is tired. These measures simply make the gunite phase go more smoothly, which facilitates being able to shoot two pools in one day. Yes, setting the guide strings adds a step, but it really helps and is ultimately more efficient.
EXCAVATION ECHOES
We’ve also discovered when you install both gunite and pebble surfaces, there are implications for the excavation process. When digging the pool, it’s common for excavators to create a ramp out of the shallow end. As the bobcat moves in and out of the pool, it’s often dragging the tail end and creating a very slight raised area in the transition at the shallow end. It’s almost imperceptible and something no one realizes when you install the gunite, but it creates an area where the water pools later on when you’re rinsing the top layer of pebble material during the surface application. Ideally, you want to be working on a surface where the rinse water drains evenly. We quickly learned that it helps to make the excavation crew aware of the issue so they dig a pool where everything is evenly sloped toward the bottom.
In pebble applications, you want to avoid puddles, otherwise you’re having to using sponges or blowers to move the water. That’s a significant issue in the surface application phase, but easily remedied when you coordinate the excavation and gunite installation. That’s a long explanation of a very simple thing: In the excavation and gunite phase, you want to make sure there are no low spots in the contours of the shell.
For us, that issue has reinforced the importance of creating a nicely sloped bottom and gently sweeping radii when transitioning from walls to the floor. We’ve found that tight radii tend to create spots where the water used in the surface application will puddle, which can create havoc in the surface installation.
We now we ask for at least a 2-inch radius on every surface transition; on steps, benches and especially in coves, we recommend at least a 6-inch radii. That sounds like a small detail, but it translates into tremendous efficiencies and cost savings in both the gunite and surface installation process.
These are all simple, basic fundamentals, but they’ve became much more important to us — and made us far more efficient and effective — in performing both the gunite and surface application phases.
Comments or thoughts on this article? Please e-mail [email protected].