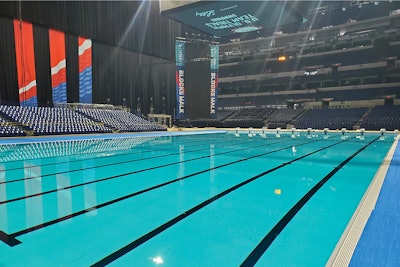
So you're a veteran pool builder; you know your craft. You've solved some problems — with pipe runs and equipment, with drainage and soils, with slopes and access and trees and enormous boulders nobody knew were there until you hit them with the bucket of a backhoe. And you've got some commercial experience, too. You've built a few community pools and seen those challenges.
With all that in mind, as a pleasant, professional exercise, take the ultimate pool building challenge: that which faced Myrtha Pools' Chief Technical Officer John Ireland this summer. He led construction of the pools for the U.S. Olympic Swimming Trials at Lucas Oil Stadium in Indianapolis.
It would be the first Olympic swimming event in a football stadium, to be held before the biggest crowd to ever witness such an event. The job would be two pools — a 10-lane, 50-meter pool for racing, another L-shaped pool with 18 lanes for warming up — plus surge tanks, for a total delivery of more than 2 million gallons of pristine swimming water, plus decking and surrounds to transform the venue into a primetime stage for USA Swimming.
That's the challenge. And there's a bit of a time crunch. You have 14 days, start to finish, green turf to clear water, plus decking, scoreboards and lights.
START AT THE BOTTOM
As a professional builder, your first thought is not of what the viewer will find pleasing to the eye, but of what will hold up the enormous weight of this pool. If it was a backyard, you'd probably be taking samples, looking for competent soil.
Here, you have an indoor stadium floor — concrete covered by artificial turf. It's used to bearing the weight of Colts all-pro defensive tackle, DeForest Buckner, about 300 pounds. But that's nothing compared to the weight of an Olympic competition pool which is more than 3500 tons.
"Not as big a problem as you might think," says Ireland. "Most arenas or even warehouse spaces list their floor loading capacity at about 350 pounds a square foot. But that's bull. They can take more. I mean, this is an 18-inch slab. With the pool filled, we've got an average of around 800 pounds per square foot, but in certain places there are much higher loads from other things than the pool. Like for instance, there's a 60-foot camera tower that's applying more load to the floor. So it's not really a problem."
Under the pool, Ireland's biggest concerns are fairly pedestrian: 1) The turf has to come out, which the stadium conveniently planned to replace anyway; and 2) There are airlines in the slab that will have to be protected with steel plates.
So far, so good. Right away, you yank out the turf and immediately start to erect a steel balance frame upon which the pool will sit. It's a special design from Myrtha. It helps to absorb stresses from the buttresses sticking out from the sides of what's going to be a gigantic aboveground pool. The frame bolts and straps together quickly, giving a firm foundation for the pool.
Everything is streamlined to only what is essential. Anything else wastes time and money, and both are in short supply. So there will be no structural connection between the pool and the floor. The pool will be held in place by its massive, distributed weight. "If you had a big enough truck, you could pull it around the stadium," Ireland says.
Snapshots from the epic build. In the photo above, you can see the warm-up pool taking shape at left, and the competition pool taking shape at right, the deck halfway done. At the near edge of the competition pool, notice the buttresses on the exterior of the pool panels already bolted into the balance frame. On the pool floor, panels are being bolted together, which will be covered by a vinyl liner, which is completely installed on the warm-up pool at bottom.
ONE MORE THING
One thing I forgot to mention. You remember the tight two-week schedule to get everything trucked in, set up, and ready for the U.S. Olympic Swimming Trials? Well, after that eight-day competition, everything has to fly out of here fast so the stadium can get ready for NFL football. And everything has to be recycled, and the pools have to find a new home because frankly, USA Swimming can't afford to buy these pools. They're just renting them.
"Even though they're selling tens of thousands of tickets for the trials," Ireland says, "the only way to make the trials financially feasible is if these pools find a permanent home somewhere else."
The actual owner of the main competition pool is a private swim club in Fort Wayne, Ind. And that's where it's headed directly after the Indy Trials. That club is going to use the pool as the foundation of a public-private partnership to develop a natatorium over the next couple of years. The pool has some cachet, having hosted swimmers such as Olympic champions Katie Ledecky and Caeleb Dressel, which will help with fundraising.
While the main pool is going north, the warm-up pool is going south to the new national training center in the Cayman Islands. These same aboveground pools in Indy will become inground pools in the Caymans and Fort Wayne. So that necessitates modular steel sections, trucked in and fitted together, piece by piece. And as soon as the event's over, you break it down, repack it into containers, and ship it to the new home where they'll rebuild it and surround it with dirt and a new deck.
"That modular steel technology really, really lends itself well to temporary pools like these in Indy," Ireland says with an engineer's admiration for an elegant solution.
The panels stand as tall as the height of the pool [8.2 feet in this case], and a little over 3 feet wide. They connect with each other, and the frame underneath with bolts, and they're supported by struts and buttresses.
"In a permanent Myrtha pool, the wall panels are made of joined, rigid PVC sheets. We use a patented process of burning PVC into steel. That's how we build all our pools. So in a normal pool, those panels show up on site already laminated in steel, and we bolt them together and then chemically seal them. We apply an organic solvent and permanently melt the panels together.
"We don't do that in temporary applications like this one at Lucas Oil because you could never get it apart. I could unbolt it, but you cannot break it apart, it's a permanent chemical weld. So for these temporary pools, because they're being resold, we use a bag liner inside the panels, which ultimately is the waterproofing surface. When the trials are over, that liner will be taken out and ground up and recycled into commercial carpet backing.
"And the new owners of the pools, in Fort Wayne and the Caymans, are getting essentially brand new equipment that has never touched chlorinated water."
BIG DECK
With the pool walls up, it's probably time to think about the deck. You've done decks before. This deck will be a little different, since you're building an aboveground pool. The rim is about 9 feet high off the stadium floor. You can't have people climbing up there to dive in.
No, you're going to need a huge deck that runs up to the edge of the pool — a supported surface extending from the pool's edge all the way to the stadium seats. Twelve rows of stadium seats will have to be removed, and by the time you're done, you'll have built over 50,000 square feet of decking and the steel supports that hold it up and make it solid.
FILTRATION AND TREATMENT
All this and we haven't even brought in a drop of water. We'll use municipal water, straight from the hydrants outside the stadium in downtown Indy, more than 2 million gallons of it. As you know, water quality will be one of the crucial KPIs, the thing everybody sees. People want crystal clear water at an Olympic event. And remember what happened at the Rio Olympics in 2016 with the green pool? Yes, well, enough said about that.
"Yes, water quality is absolutely one of the most important factors," Ireland says. "And that's tricky because we're dealing with tight time constraints. By the time we fill these pools, theoretically, we might only have one or two cycles for the filters before we need to have HDTV-quality water ready."
That sentence alone could make a pool pro break out in sweat. What will we use for filtration? You can forget about any kind of high-rate sand filter with enhanced media, because you're on the 40-yard line of a football stadium. You can't backwash thousands of gallons of water. Nowhere to put it. At the same time, you need super fine, particulate filtration. They've got underwater cameras broadcasting to the world. You need to be able to see the swimmer in lane six.
"We exclusively use regenerative media filtration for that reason. It just filters a smaller particle. And as you say, not having to backwash is very important," Ireland says.
"Also, from an HVAC perspective, this space is not intended to be a pool space, so we need to take careful consideration of the water chemistry because we cannot be generating any chloramines. So we'll use Pulsar dry chlorine feeders with full bypass UV. And then for pH control, we'll have both bulk CO2 and muriatic dosing."
"All that's running through a combination of Schedule 80 PVC, and then some CPVC, because we also have to heat 2 1/2 million gallons of water. We're commingling the water for both pools through some pretty massive heat exchangers. We're actually piggybacking off the building's boiler systems to heat the pools."
Filling the U.S. Olympic trials competition pool at Lucas Oil Stadium. A triumphant pause in the hectic 2-week project.
CURRENT AFFAIRS
For Olympic swimming, there's another big consideration you don't have at the local YMCA — currents. You have to design and plan circulation so there's never so much as a whiff of a current that could slow swimmers by a hundredth of a second, and thus, potentially, cheat them of victory. That starts with the inlets.
"Myrtha has developed an inlet system that runs through the sidewall using very large diameters — 3 and 4 inches — that allow you to use laminar flow. So because we're not using a dispersion principle, like all conventional inlets, we're able to push water over great distances at very low velocities.
"The entire pool has been modeled using computational fluid dynamics to completely predict exactly how it's going to recirculate and ensure we're not generating currents that might affect swimmers. And once it's built, we field test it to verify that before the event, using international standards that we helped develop with world aquatics."
After all that complexity and CFD, the pump schedule itself is pretty straightforward. Full power all night to maximize clean, and then when it comes to race time, cut the engine.
"At night, we're running at almost 4,000 gpm to turn the pool over as many times as possible for the next morning. And then right before athletes go into the water, we drop those flow rates down to under 1000 gallons a minute so that we're minimizing any disturbance."
EVERYTHING AT ONCE
The hard part, according to Ireland, isn't the shell or the deck. It isn't supporting the staggering weight of millions of gallons of water. It isn't the water treatment or line velocities needed to transport enormous volumes yet produce no current at race time.
It's going from absolutely nothing to perfect in two weeks, with no margin for error. It's building two large, high-tech pools mid-field of an NFL stadium, the largest swimming venue in the history of the sport, in 14 days, and getting it all right.
"The issue with any of these temporary builds is you're taking nine months of construction and compressing it into just a couple of weeks. So it's really a ballet of organization for a small army of people, all working 18-hour days. The local unions provide hundreds of skilled workers to help supplement our crews and the crews of the other builders. For an event like this, we'll plan for two years.
"Multiple companies all have to interact efficiently, on a tight schedule, and they have to get things done at the same time because in addition to building a pool, you're basically putting on a rock concert. There are 110,000 pounds of lighting rigs going up. You have to build a whole new scoreboard just for the event. And all of that needs to happen almost simultaneously and to tight tolerances — 5 mm for the pools. And in addition, for everything, you've got to justify the expense."
INFINITE SOLUTIONS, AND ONE THAT WORKED
And that is how Myrtha Pools and John Ireland solved the ultimate pool building challenge. Of course, there are an infinite number of solutions to any problem, and builders reading this will have their own ideas, but the Myrtha plan worked to perfection in the crucible of real life. The 2024 U.S. Olympic Trials went off with a bang, and the aquatics performed perfectly.
Like any great construction project, the historic pool build at Lucas Oil Stadium was achieved with great concert of action, combined with intense focus. But what about the pressure? For Ireland, everything had to work flawlessly and on schedule or it would all be his fault.
"If I can be perfectly honest," Ireland told the Indy Star, "it scared the s—t out of me."
This article first appeared in the August 2024 issue of AQUA Magazine — the top resource for retailers, builders and service pros in the pool and spa industry. Subscriptions to the print magazine are free to all industry professionals. Click here to subscribe.